Six Sigma är det? Projekt som process eller process som projekt
1986 var Motorola så plågad av en tillverkningsfel att dess ingenjör, Bill Smith, kom med en metod för att minska defekterna till matematisk felaktighet. Så det dök upp Six Sigma -metoden, som andra industri- och finansjättar snart kommer att beväpna sig.
Six Sigma är ett begrepp från sannolikhetsteorin, uttryckt med formeln: högst 3,4 defekter per miljon produkter eller processer. Metodens matematiska uppgift är att minska spridningen av alternativ.
Det vill säga bokstavligen 6 Sigma är en metod för projektledning som fokuserar på att eliminera tillverkningsfel som en klass.
Principer
- Gör processer förutsägbara
- Försök att säkerställa att produktions- och affärsprocesser kan beskrivas, mätas, analyseras, förbättras och kontrolleras
- För att lyckas med Six Sigma, involvera alla människor i organisationen, särskilt högsta ledningen.
- Sätt upp specifika mål som kan beräknas eller mätas: minska kostnaderna med 20%, öka lönsamheten med en tredjedel, minska produktionscykeln med en timme
- Locka chefer med starkt ledarskap och lyssnande
- Ta beslut baserade på bevisad information och statistik snarare än gissningar.
Algoritmer
Six Sigma erbjuder två metoder, beroende på om du förbättrar processen - DMAIC eller skapar en ny produkt - DMADV, aka DFSS. Båda metoderna kan beskrivas med formeln Planera-Gör-Kontrollera-Fix.
- Definiera projektmål och kundbehov. Bilda ett projektteam, upprätta sitt ansvarsområde och tilldela auktoritet.
- Samla aktuell data, "mäta" viktiga processparametrar.
- Analysera den insamlade informationen och identifiera de faktorer som påverkar organisationens kvaliteteller affärsverksamhet. Hitta den främsta orsaken till äktenskapet och defekter, föreslå metoder för att eliminera det.
- Förbättra eller optimera dina nuvarande processer. Gör prövningsändringar.
- Övervaka dina redigeringar så att eventuella avvikelser från målet inte igen leder till defekter. Rapportera projektets framsteg på informationstavlor, se hur de arbetar med statistik. Upprepa processen tills du når önskad kvalitet.
Huvudprincipen för DMAIC är att vara proaktiv. Nya konsumentpreferenser måste förutsägas, defekter måste förebyggas.
DMADV- eller DFSS -algoritm
- Definiera mål som ska överensstämma med kundens önskemål och affärsstrategi. Skapa ett projektteam.
- Ange produktens huvudsakliga egenskaper, behoven för produktionscykeln.
- Hitta och analysera flera alternativ.
- Välj det bästa alternativet och börja arbeta med det.
- Genomför ditt projekt i praktiken.
Verktyg
Både kvalitetshanteringsprinciper och statistiska metoder kan användas. De första är:
- "5 varför". Vi ställer denna fråga tills vi får reda på huvudorsaken till defekterna.
- Vi skisserar vilka resurser vi har och vad som behöver göras. Här är till exempel en karta över processerna vid beställning och frakt av varor:
- Kostnads -nyttoanalys. När det finns flera projektalternativ, välj det med bästa nytta-till-kostnad-förhållandet.
- Kvalitetskritiska mätvärden (CTQ -träd). Rita ett diagram över de viktigaste egenskaperna för ditt projekt. Här är till exempel ett träd för att skapa en barnklädbutik.
- Planerar ett experiment. Hjälper till att bedriva forskning mer effektivt och förbereda sig för experiment.
Statistiska verktyg inkluderar:
- ANOVA
- Regressionsanalys
- Sprida diagram
- Shewhart kontrollkort
- Pareto -kurva.
Hierarki
Begreppet ledning påminner om orientalisk kampsport. Rollen som artisten beror på hans bälte - kunskapsnivån och färdigheterna hos Six Sigma.
- På toppen av pyramiden är Huvudledarskap ... Det fördelar ansvar och resurser.Huvudledarskapbryter ner interna hinder och bekämpar personalens medfödda motstånd mot förändringar.
- Mästareimplementerar metodiken i organisationen och mentorer ägarna Svarta bälten.
- Black Belt Mastersövervaka distributionen av Six Sigma och leda de vanliga svarta bälten.
- Svarta bältenunder överinseende av mästare är de engagerade i ett projekt och utför uppgifter som tilldelats dem;
- Gröna bälten- det är personal som utöver sina arbetsuppgifter arbetar med implementering av metodiken. Följ detta Svarta bälten.
- Ibland isolerade Vita bälten och Gula bälten - anställda på företaget som känner till Six Sigma på initialnivå och antingen delvis deltar i projektet eller följer erfarna kollegors handlingar.
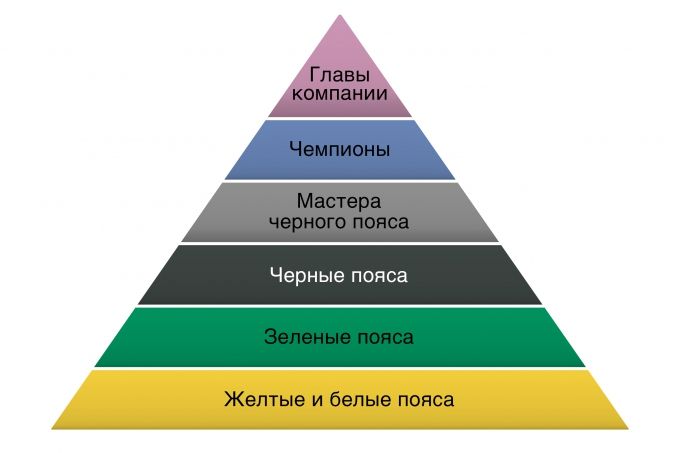
Du kan bli certifierad i företag och. Träning sker både lokalt i USA och online. Du kan också ta tentor från din dator genom att installera speciell programvara.
Certifikat utfärdas också av utvecklaren av metodiken, företaget. Utbildningskurser hålls inte bara i Nordamerika, utan också i Europa, Asien, Afrika.
Skillnader från liknande metoder
Sedan slutet av 2000 -talet. blev populär metodik - en kombination av metoder Lean, lean manufacturing och Six Sigma. Leans uppdrag är att sänka kostnaderna och säga adjö till arbetsflöden som inte ger värde för konsumenten. Det hjälper också till att standardisera produktionen.
Six Sigma -metoden syftar till att minska defekter och kräver ökad processkontroll. Six Sigma, med sin statistiska analys, är praktiskt taget en teknisk disciplin i jämförelse med Lean, vilket innebär mer visuell kontroll och förändrar arbetsplatsens organisation.
Six Sigma och Lean jämförs med en annan metod (för många är det mer en företagsfilosofi) -. Det kräver också att organisationen ständigt förbättrar och standardiserar processer. Den största skillnaden för Kaizen är dock tyngden på snabba och enkla lösningar som diskuteras öppet med personalen.
Brister
- Fler och fler organisationer började utbilda framtida Black Belt -innehavare ... Som ett resultat säger kritiker att kvaliteten på certifieringen har sjunkit. Svarta bälten släpps med mindre kunskap.
- Fortune -tidningen hävdade att nästan alla de 58 stora företag som lovade Six Sigma -lojalitet sedan hoppade av S&P 500. Six Sigma Methodology,journalister i affärspublikationen insisterar, hjälper inte att skapa genombrottsprodukter och teknik.
- Detta kan bero på en annan nackdel att Six Sigma krediteras för att begränsa kreativ frihet. Enligt denna åsikt tillåter inte konstanta "mätningar" och statistisk analys projektgruppen att komma med brainstorming och komma med en oväntad idé. Metoden har en rigorös algoritm och driver främst kommersiella mål, inte innovativa.
- Sex Sigmas gömningar i statistik har också varit föremål för kritik. Teoretisk kontrovers raser kring vissa instrument som kanske inte helt överväger risker.
Vad är Six Sigma i Time Management?
Six Sigma metodhöjdpunkter två gånger - ledning och cykeltid.
- Ledande tid talar om hur mycket som har gått sedan kundens begäran och mottagandet av produkten / tjänsten.
- Cykeltid betyder det antal timmar det tar att slutföra en produktionscykel eller arbeta med en process.
EDR är ett amerikanskt företag som tillåter online att lösa juridiska frågor relaterade till fastigheter, från köp / försäljning till utfärdande av certifikat. Hennes kunder inkluderar advokater, försäkringsgivare, myndigheter, fastighetsmäklare och värderingsmän. Företaget har satt upp ett mål att förbättra ledtiden - att tillhandahålla tjänsten inom 24 timmar från det att begäran mottogs. För detta användes Lean Six Sigma -metoden och DMAIC -algoritmen.
I EDR -programvaran fungerade automatiska räknare, som registrerade hur lång tid en viss process tog. Beräkningar visade att ledtiden i företaget är 50,1 timmar - dubbelt så lång som det fastställda målet. Om projektet lyckas kommer EDR att spara 1 miljon dollar per år.
Steg 2 - Datainsamling
Under analysen av data fann Black Belts följande defekter:
- Personalen formulerade inte exakt vad de ska tänka på i körtiden. Till exempel om man ska inkludera lunchrast och semester.
- Kunder skickade ofta förfrågningar utanför öppettiderna, vilket inte spårades av systemet. Det visade sig att räknaren inte spelade in några förberedande processer, och ledtiden i företaget varar ännu längre än 50,1 timmar.
När projektledarna (PM) ställde in mer specifika parametrar för nedräkningen var ledtiden 67,5 timmar. Ändringen i det statistiska tillvägagångssättet passade dock inte aktieägarna och personalen i EDR. Den föregående ledtiden påverkade direkt priserna på tjänster och personalpolitik. De anställda ville inte acceptera den nya metoden för att bedöma sitt arbete och ville arbeta som tidigare.
Dessa psykologiska svårigheter löstes när PM började regelbundet kommunicera med ledning och personal för att arbeta tillsammans om nya idéer.
Steg 3 - Analys
PM använde Ishikawa -diagrammet, felläge och effektanalys och Six Sigma "5 Why" -metoden för att markera eventuella defekter:
- För många förseningar mellan arbetsflöden
- Vissa processer tar för lång tid, vilket ökar ledtiden i allmänhet.
- Kundförfrågningar tas emot utanför kontorstid och kan komma att behandlas senare än nästa dag.
- En applikation kräver flera olika processer, vilket ökar ledtiden i denna situation
- Information från databasen finns i olika filformat, och några av dem är svåra att bearbeta
- Enskilda förfrågningar passar inte in i standardprotokollet och kräver personlig inblandning från IT -avdelningen
- Anställda "sprider" mottagna ansökningar och löser dem inte direkt.
4 och 5 steg - Förbättring och kontroll
PM kontrollerade alla möjliga defekter och drog slutsatsen att det viktigaste problemet var de långa intervallerna mellan arbetsprocesser. Dessutom översteg tiden mellan operationerna den tid det tog att arbeta.
Därför har PM: er fördelat ansvar så att en medarbetare nu kan utföra flera processer och inte vänta på att hans kollega ska klara sin uppgift. Denna åtgärd förbättrade organisatorisk flexibilitet och underlättade monotonin i arbetsflödet.
PM presenterade pilotprojektet för ledning och personal. Efter de anställdas kommentarer och önskemål ändrades planen. Artisterna genomgick ytterligare utbildning innan räknarna slogs på igen. Projektet visade sig vara framgångsrikt: ledtiden varade nu 23 timmar.
Vad är Six Sigma i industrin
Asahi India är det indiska dotterbolaget till det japanska företaget Asahi. Dotterbolaget tillverkar glas till bilar. En av modellerna, ME3 bakluckeglas, tillverkades med ett genomsnittligt skrot på 86,8%. Styrelsen satte upp ett mål att minska risken för defekter, och teamet för projektledning (PM) kom igång.
Metoden med sex sigma, nämligen DMAIC -algoritmen, var tänkt att rädda situationen. Produktionsprocessen skedde i tre steg:
- Förberedande skede ... Glaset fick önskad form, varefter kanterna polerades, tvättades, torkades och inspekterades.
- Täta ... Speciellt bläck applicerades på glasytan, som sedan torkades i ugnsfacken. Denna beläggning skyddar mot solens strålar.
- Härdning och bearbetning ... Glaset värms upp till önskad temperatur, böjs till en förutbestämd form och kyls med en högtrycksluftström. Därefter undersöks det och skickas till försäljning.
Steg 1 - Lär känna projektet
Tillverkningsfelet började med köpet av en universalugn, vilket moderbolaget insisterade på. Den nya utrustningen var tänkt att göra glas för både sido- och bakdörrarna på bilen. Bakrutorna visade sig dock vara mycket mer defekta än förväntat och var inte alltid nöjda med konsumenternas kvalitet.
Tre steg i produktionsprocessen kom ut med följande procentandel av defekter:
Förberedande skede - 1,5%
Utskrift - 1,5%
Härdning och bearbetning - 10,5%.
Företagets ledning förväntade sig att dessa siffror skulle vara 0,5% för de två första etapperna och 6,5% för det sista.
Projektgruppen gjorde ett diagram där produktionen sönderdelades i små processer och identifierade följande defekter:
Bearbeta |
Defekt |
Beskrivning |
|
Förberedande |
Avbrutna |
Smula skalar av kanterna |
|
Kanterna klipps i kontakt med slipskivan |
|||
Fel |
Delvis slut på bläck på ytan |
||
Dammig mark |
Dammpartiklar träffar den tryckta ytan |
||
Härdning och behandling |
Ugnstryck |
Främmande partiklar finns kvar på glaset |
|
Förstörelse från luftflöde |
Glas bröt i små fragment under kylning med högtrycksluft |
||
Fel böjning |
Glaset är inte böjt till önskad form |
Steg 2 - Datainsamling
PM: n sammanställde en orsak och verkan -matris för att identifiera sambandet mellan produktionsprocesser och output. Det ger 3 betyg: 1 - svag korrelation, 3 - medium korrelation och 9 - hög korrelation.
Det visade sig att under härdning och bearbetning, det mest problematiska stadiet, kan defekter associeras med temperaturen i vart och ett av ugnens fyra fack, glasets temperatur och ugnens hastighet.
Steg 3 - Analys
PM tittade på nästan tusen glasformar på en dag och inspekterade dem var halvtimme under produktionen. Detaljerade mätningar gjordes för varje produktionsparameter. Statistisk analys har identifierat rotorsakerna till defekterna.
Som varnat av orsaken och verkan -matrisen, under härdning och bearbetning, uppstod avslag på grund av avvikelser i ugns- och glastemperaturer, liksom på grund av produktionslinjens hastighet.
I förberedelsestadiet uppstod defekter på grund av överdrivet tryck på materialet, felaktig fixering och överdriven kraft hos skärutrustningen. Under utskriften orsakades problem av våtfilm, för torra temperaturer, bakladdningsplatta i maskinen och otillräckliga distanser i glas.
Steg 4 - Förbättring
PM genomförde planeringen av experimenten. Ett särskilt komplex valdes ut för varje steg i produktionsprocessen.
För det förberedande skedet utarbetades 16 nya lösningar. PM experimenterade med skärutrustningsinställningar och fixeringsparametrar. Som ett resultat sjönk defektgraden till önskad 0,5%.
Under utskriftsfasen experimenterade designteamet med distanstjocklek och temperatur. Som ett resultat minskades också andelen defektivitet till 0,5%.
Under härdningen och bearbetningen av PM genomfördes 400 iterationer för var och en av de 16 varianterna för att uppnå förbättrad prestanda. Teamet beräknade den optimala temperaturen för vart och ett av ugnsfacken och rätt hastighet för produktionslinjen.
Nu har avvisningsgraden sjunkit till 3%, vilket visade sig vara ännu bättre än det uppsatta målet på 6,5%.
Steg 5 - Kontroll
Minskningen av defekt hade ännu inte konsoliderats. PM utarbetade en kontrollplan som angav nödvändiga parametrar för ugnen och produktionslinjen. De delade också ut vem som ska övervaka processerna, hur ofta de ska göra det och vilka mätinstrument som ska användas för detta.
Ansökan från stora företag
Six Sigma -metodik utvecklades i företaget Motorola... Hennes ledarskap var missnöjd med att 5-10% av de årliga intäkterna läggs på att bekämpa äktenskap och dess konsekvenser. Med Six Sigma sparade Motorola 16 miljarder dollar från 1986 till 2001.
Sedan dess har metoden antagits av många industriella och finansiella tungviktare. Biltillverkare Vadställe tack vare Six Sigma ökade det sina intäkter år 2000 med 300 miljoner dollar. Företaget spenderade flera miljoner på att utbilda sin personal i metodiken och ångrade sig inte. PM har skapat ett antal framgångsrika projekt som har glatt Ford -kunder.
General ElectricÄr ett av de första företagen som använder Motorolas utveckling. Verkställande direktör Jack Welch började utbilda personal i Six Sigma 1995. I 13 dagar och 100 timmar gick cheferna igenom ett rikt program. Grönt bälte blev ett krav för marknadsföring och framgångsrikt genomförande av metoden ökade premien med 40%. Högre ledning kom ofta till föreläsningar för att personligen svara på personalfrågor.
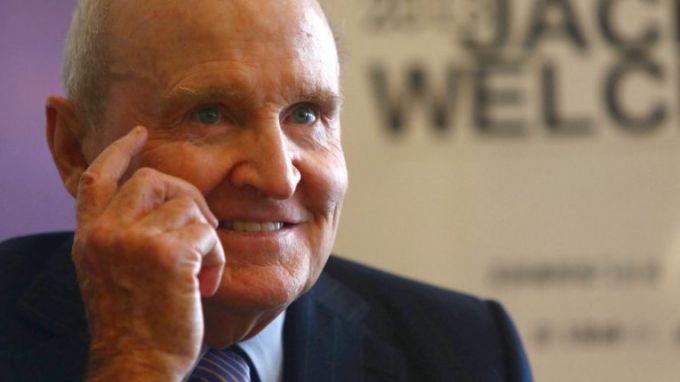
General Electric har investerat inte bara i utbildning av sina egna anställda, utan också i outsourcingföretag. Redan 1997 ökade GE: s företagsvinst med 700 miljoner dollar. Under programmets tre år fick företaget ytterligare 4,4 miljarder dollar.
Tredje största bank i USA Amerikanska banken använde Six Sigma -principer 2005 för att minska den tid det tog att öppna ett internetkonto. Antalet kundsteg minskade från 10 till 4. Det blev lättare för användare att logga in, de har nu online textstöd. Som ett resultat ökade antalet lån och insättningar kraftigt och banken ökade sin vinst med 30%.
Flygplanstillverkare Boeing 1999 startade en storskalig utbildning av personal i principerna för Six Sigma. Företaget har producerat cirka 60 svarta bälten och över 300 gröna bälten. Boeing har sänkt kostnaderna med 210 miljoner dollar på fem år.
År 2007 implementerade 82 av de 100 största amerikanska organisationerna Six Sigma -principer. Många av dem har varit ledande inom sin bransch och internationellt. Här är en studie som bevisade att företagen fick ytterligare 1-7% av vinsten under fyra års implementering.
TOPP -företag och deras vinst med Six Sigma
Lanseringsår Sex sigma | Företag | Typ av verksamhet | Intäkter 2008, miljoner dollar | Kvantitet arbetare |
Tillverkning av mobiltelefoner | ||||
Bygg, projektledning | ||||
automatisering och kontroll | ||||
Produktionsutrustning | ||||
Kemisk industri | ||||
Läkemedel | Okänd |
|||
Banksektor | ||||
Autoproduktion | ||||
General Electric | Tillverkning av maskiner |
TOPP -företag och deras besparingar med Six Sigma
Företag | Observerad period | Totala intäkter för den observerade perioden, miljoner dollar | Sparat belopp, miljoner dollar | Sparat belopp,% av intäkterna |
General Electric | ||||
Böcker
Lösa komplexa industriproblem utan statistik / Ralph Polak, 2016
För de Six Sigma -adepter som inte är särskilt starka i den matematiska delen av metodiken. I stället erbjuder författaren 14 praktiska exempel där han lär ut ”kvalitetstänkande”. Polak avslöjar hur man snabbt kan skilja mellan dålig och bra produktion och hur man visuellt hittar "ledtrådar" som leder till orsakerna till defekter. Behandla kvalitetsanalyser som en brottsplatsundersökning, författaren instruerar oss.
Six Sigma Way. A Practical Guide for Implementation Teams / Pete S. Pandy, Robert P. Newman, Roland R. Caveneg, 2005
Skriven av tre tränare som arbetade för General Electric. Den förklarar hur du använder Six Sigma -verktyg och mallar för att samla information, förbättra produktiviteten och minska kostnaderna.
Lean Six Sigma / Michael L. George, 2007
Författaren grundade sitt eget konsultföretag, där han implementerade management baserat på idéerna från Six Sigma och Lean. George beskrev hur han kan förbättra produktkvaliteten och minska släpptiden med två metoder.
Six Sigma for Dummies / Craig Gigi, 2008
Traditionellt för nybörjare, där metodikens grunder förklaras på ett enkelt språk.
Program och program
Saas-service av projektledning, vilket tillåter hantera projekt, uppgifter och checklistor. Alla principer för intuitiv visualisering, Gantt -diagrammet och Kanban -kort är implementerade här (från och med oktober 2017 är det redan i betatestning).
Med Worksection är det bekvämt att hålla koll på lagaktivitet och hela projektets framsteg. Använd Six Sigma -verktyg:
- förskriva förbättringsplaner i uppgifter med checklistor eller deluppgifter
- markera de ansvariga för uppgraderingar, övervaka framsteg och slutförande i realtid
- analysera resultat i rapporter, implementera framgångsrik teknik
- ange budget och utgifter för experiment direkt i uppgifterna.
Ansökan om iOs. Skapa grafer, mäta prestanda, använd statistiska verktyg, skapa snabb åtkomst till dokument och kika på definitioner av termer.
Ett program för iO: er som visualiserar arbetsflödet. Skapa kort där du kan tilldela rollerna som artister, samt lämna kommentarer och förslag. Bekväm spårning av genomförandet av processer.
Ansökan om förberedelse inför tentor vid ASQ. Innehåller 300 frågor för kandidater i Svarta bälten och gröna bälten ... Stöds av Android och iOs.
Integreras i Microsoft Excel. Innehåller grundläggande Six Sigma statistiska verktyg.
Dom
Six Sigma är en strategi som lär dig hur du letar efter defekter och deras orsaker i organisationen.
För detta används statistiska verktyg, experimentplanering och kontinuerlig kvalitetshantering. Framgången för Six Sigma -applikationen beror på utbildning av projektledare och deras interaktion med personalen.
Som beräknat i väst kan en välutbildad svartbälthållare göra fem eller sex projekt på 12 månader. En sådan specialist kommer att spara organisationen 175 tusen dollar och lägga till 1 miljon dollar till årsvinsten.